specification
Accuracy of Spinneret
Surface Roughness of Spinneret Hole (ISO)
-
1、countersinkN5-N7
-
2、counterboreN3- N6
-
3、transition angleN2-N6
-
4、capillaryN1-N6
Surface Roughness of Exit Side (ISO)
-
1、mirror finish by buffingN1
-
2、mat finish by lappingN2-N4
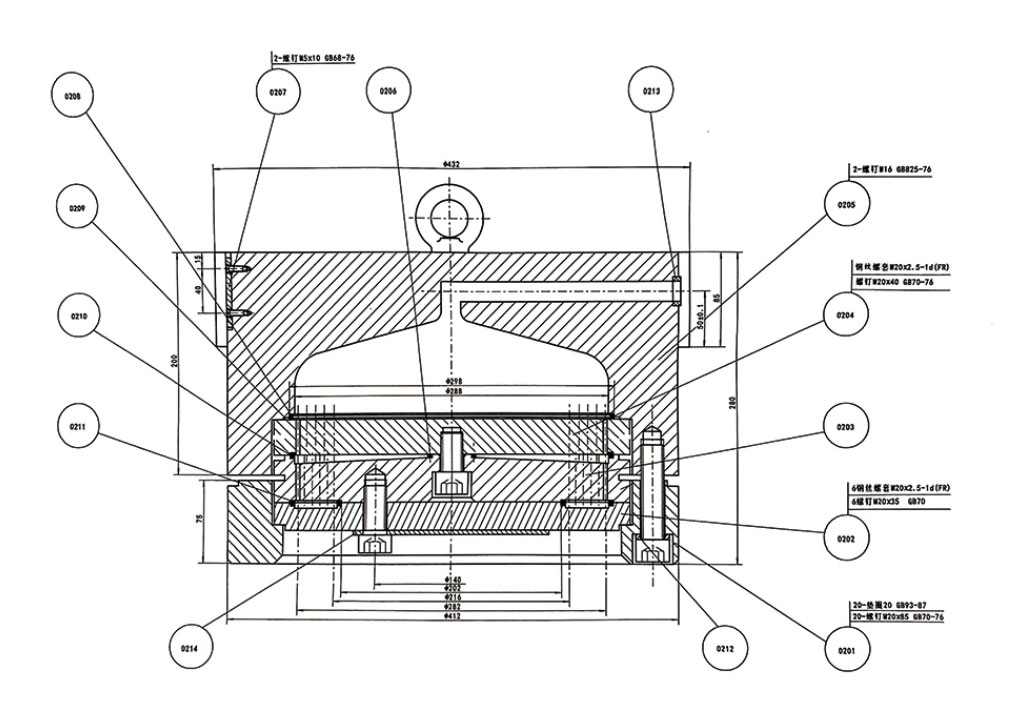
Tolerance of capillary
Round Hole Spinneret
Diameter of Capillary D |
Length of Capillary L |
Tolerance of D | Tolerance of L | ||
---|---|---|---|---|---|
Special | Precision | Special | Precision | ||
f0.04 - f0.10 | ≤1.00 | ±0.001 | ±0.002 | ±0.01 | ±0.02 |
f0.11 - f0.20 | ≤3.00 | ±0.002 | ±0.002 | ±0.01 | ±0.02 |
f0.21 - f0.50 | ≤5.00 | ±0.001 | ±0.002 | ±0.01 | ±0.02 |
f0.51 - f1.00 | ≤8.00 | ±0.002 | ±0.004 | ±0.02 | ±0.04 |
Profiled Hole spinneret
Width of slit W |
Length of capillary L |
Tolerance of W | Tolerance of I.r,d,g.a | Tolerance of L | |||
---|---|---|---|---|---|---|---|
Special | Precision | Special | Precision | Special | Precision | ||
0.04–0.06 | ≤5.0W | ±0.002 | ±0.003 | ±0.015 | ±0.025 | ±0.02 | ±0.03 |
0.06–0.10 | ≤10.0W | ±0.002 | ±0.003 | ±0.015 | ±0.025 | ±0.02 | ±0.03 |
0.10–0.20 | ≤20.0W | ±0.002 | ±0.003 | ±0.015 | ±0.025 | ±0.02 | ±0.03 |
≥0.20 | ≤30.0W | ±0.002 | ±0.003 | ±0.015 | ±0.025 | ±0.02 | ±0.03 |
profiled holes
SHAPES OF SPINNERET HOLE/ MATERIALS
Spinneret for Melt Spinning
Spinneret for Dry or Wet Spinning
Type contrast | AISI DIN JIS GB |
304 1.4301 SUS304 0Cr18Ni9 |
316 1.4401 SUS316 - |
316 1.4404 SUS316L 0Cr17Ni14Mo2 |
317L 1.4438 SUS3171 |
321 1.4541 SUS321 ICR18Ni9Ti |
431 1.4057 SUS431 1Cr17Ni2 |
630 1.4542 SUS630 0Cr17Ni4Cu4Nb |
Main Chemical Composition |
C≤ Cr Ni Mo Cu Ti Nb/Ta |
0.08 18-20 8-10.5 - - - - |
0.08 16-18 10-14 2-3 - - - |
0.03 16-18 10-14 2-3 - - - |
0.03 18-20 11-15 3-4 - - - |
0.12 17-19 8-11 - - 5X%C-0.8 - |
0.17 15-17 1.5-2.5 - - - - |
0.07 15.5-17.5 3-5 - 3.5 - 0.15-0.45 |
Mechanical and Physical Properties |
1000kg/m³ Density | 7.9 | 7.95 | 7.95 | 7.95 | 7.9 | 7.7 | 7.75 |
(0.2)Yield Strength 0.2% offset, MPa≥ | 196 | 205 | 176 | 176 | 205 | 588 | 785 | |
(O)Tensile Strength MPa | 496-600 | 496-600 | 480-600 | 480-600 | 496-600 | 785-1370 | 840-1370 | |
(8%)≥Elongation | 50 | 45 | 50 | 50 | 50 | 14 | 14-22 | |
Reduction of area | 60 | 60 | 60 | 60 | 60 | 45 | 52-56 | |
Hardness (solution annealed) HB | 130-180 | 130-180 | 130-180 | 130-180 | 130-180 | 250-270 | 270-290 | |
E Elastic Modulus GPa | 197 | 197 | 197 | 197 | 197 | 204 | - | |
Magnetcable | 无 | 无 | 无 | 无 | - | 有 | 有 | |
Hardness range for spinnerets HB | 130-180 | 130-180 | 130-180 | 130-180 | 130-180 | HRC26-35 | HRC28-44 |
Hardness was determined upon the heat treatment processes
(as): H900 H1025 H1075 H1150
HRC<40≥35≥31≥28
Tantalum for wet spinning
g/cm³ Density | MPa Tensile strength | (6%) Elongation | HV0.2 Hardness | HV0.05 Hardness after treatment |
---|---|---|---|---|
16.6 | 313.6 | 25 | 90–120 | 300–500 |
cleaning
Cleaning of the spinnerets for melt spinning:
To clean spinnerets, you may choose one of the following methods which we recommend:
- Calcination: In an automatic box-type furnace, the spinnerets are heated to 450–480 °C. When the temperature exceeds 480 °C, superheated steam passes through the calciner to blow out the flames and lower the temperature, so that the spinnerets can be protected from damage.
- Salt Bath: Formed by a NaNO3 (45%) – NaOH (10%) mixture (melting point 200 °C), the salt bath acts as a strong oxidant at its operating temperature of 450–500 °C. The polymer is decomposed to CO2 and H2O very quickly in 60 to 90 minutes. After processing, any remaining salts on the spinnerets should be washed away with hot water, oxides removed by dilute nitric acid, and then washed sequentially in clean water, an ultrasonic tank, and finally dried.
- Procedyne Fluid Bed: At a temperature of 450–500 °C, aluminum oxide powder is fluidized by a hot air stream and scours the spinnerets. About 70% of the polymers are detached and decomposed. A small amount of carbon becomes CO. All these, including inorganic substances such as TiO2, are discharged in the air. The advantage of this method is that the spinnerets can be cleaned automatically.
- TEG Method: First, place the spinnerets in a boiling solution containing NaOH (15%–20%) for 2 to 3 hours to remove most of the polymer, then place them in a TEG bath at 260–280 °C for about 12 hours. After cooling, the spinnerets should still be washed sequentially in alkaline solution, clean water, and an ultrasonic tank before drying and storage. The process should avoid overheating and is suitable for any type of stainless-steel spinnerets, but it takes a rather long time.
- Vacuum Calciner: By burning in low pressure and vacuum, most of the polymer can be decomposed. The remaining residue is washed out in the same furnace. The whole process can be automatically controlled and is easy to operate.